IBC TANK
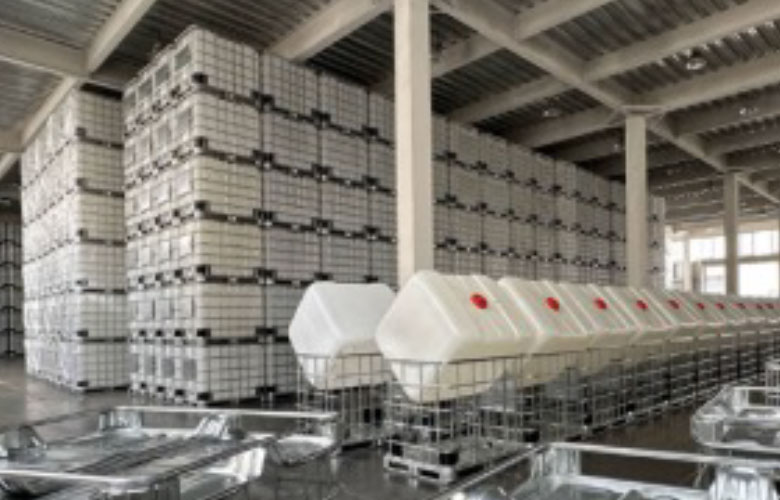
Chinese name: IBC ton tank
English name: IBC TANK
Colloquialism: Tons of tank, tons of packaging, kiloliter tank
Advantages: Light weight, high strength, corrosion resistance
Application: Chemical, pharmaceutical, food, coatings, grease, etc
Properties: IBC Intermediate Bulk Container
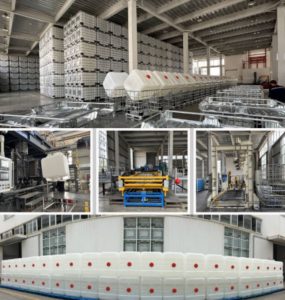
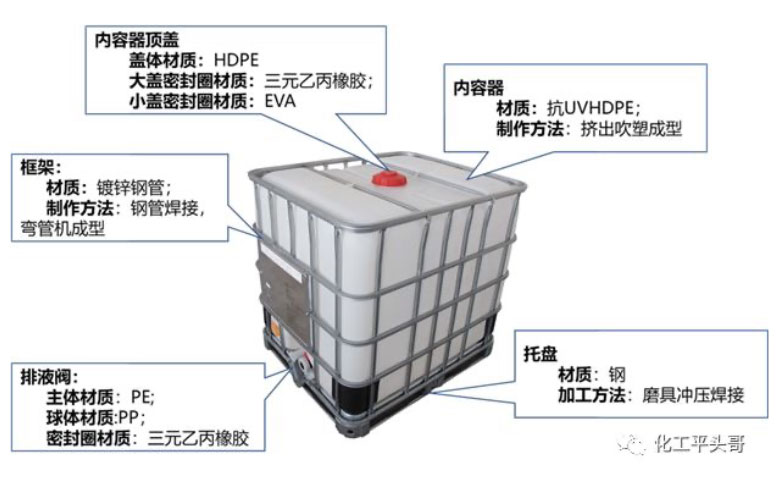
IBC tanks are a type of container widely used in industrial and commercial fields for storing and transporting liquids or bulk items. IBC stands for Intermediate Bulk Container, which is a medium bulk container. It is usually made of plastic and has certain standards and specifications.
The standards for IBC tank mainly include the following aspects:
1. Capacity: The capacity of IBC tank is usually 1000 liters, or 1000L. This capacity is common in various countries and regions, and can conveniently store and transport large amounts of liquids or bulk items.
2. External dimensions: There are also certain standards for the external dimensions of IBC tank. Typically, the external dimensions of a standard IBC tank are approximately
1200mm long, 1000mm wide, and 1165mm high. This size design can make IBC tank more stable and convenient during stacking and transportation.
3. Material: IBC tanks are generally made of plastic materials such as high-density polyethylene (HDPE) . These materials have good corrosion resistance, wear resistance, and impact resistance, which can effectively protect the liquid or items inside the container.
4. Structure: IBC tank are usually composed of a top screw cap or piston type opening, a bottom discharge port, and an overall frame. This structural design can facilitate loading, unloading, and filling of liquids or items, while also facilitating sealing and stability during transportation.
Advantage
By using container packaging, the chief mate can reduce production, storage, transportation, and operating costs. Save a lot of manpower and material resources. Compared to traditional packaging, storage can save 35% of space, and loading and unloading can be carried out using forklifts, reducing the many troubles of manual handling. Filling: 1000L tank =5 piece 200L drums, reducing the trouble of repeated operations during the filling process and avoiding waste such as material leakage and spillage.
In summary, IBC TANK are convenient to use, economical and durable. With the development of internationalization, IBC TANK have gradually become the mainstream product of liquid packaging. It can hold Class II and III dangerous goods, with a maximum liquid density of 1.5g/cm3 for Class II dangerous goods and 1.8g/cm3 for Class III dangerous goods. The product structure is reasonable, firm and sturdy, and can be directly loaded and unloaded by forklift, and can be stacked for storage. The bottom of the product is equipped with a drain valve, which facilitates, quickly, thoroughly, and safely discharging the liquid. It is easy to clean, can be reused multiple times, saves energy, and is beneficial for environmental protection
1000L IBC TANK
MODEL | (L) | WEIGHT(kg) | SIZE(mm) | DESITY | PALLET TYPE |
1000 | 1058 | 56 | 1200x1000x1135 | 1.9 | 全钢托盘 |
1000 | 1058 | 62 | 1200x1000x1135 | 1.9 | 全钢托盘 |
IBC TANK is designed to adapt to the packaging, storage, and transportation of various liquid products in accordance with international maritime safety regulations, relevant national laws and regulations, and industry standards. This product is formed with good hygiene, comprehensive mechanical and physical properties, and inherent mechanical principles. The product ensures corrosion resistance to acids, alkalis, oils, and other liquids, and has advantages such as transportation, convenient use, and safe storage. It is suitable for highways, railways, and other industries Water (sea) transportation is more suitable for standard container exports. This product can be widely used in liquid manufacturing industries such as petrochemicals, dyes, intermediates, pesticides, brewing, daily chemicals, beverages, etc. It is used as a storage and transportation packaging for Class II and below dangerous goods and ordinary liquid products.
IBC TANK is blow molded using ultra-high molecular weight high-density polyethylene (HWHDPE). Axial and radial wall thickness control is used to ensure that the wall thickness of the container is relatively uniform at the symmetrical part. UV resistant agents are added to the raw material of ultra-high molecular weight high-density polyethylene (HWHDPE) to prevent aging of the container liner. There is a liquid level mark on the side of the container for easy filling. The discharge valve is made of high-density polyethylene (HDPE) and polypropylene (PP), and is connected to the container inner liner with screw teeth. EPDM or fluororubber (FPM) is used to adapt to the corrosion resistance of various liquid products. The valve handle is equipped with safety screws to prevent accidental opening. The valve outlet is equipped with an inner cover and sealing ring, and is fixed externally with a threaded cover as the secondary seal of the valve to prevent valve leakage. The upper part of the container inner liner is a filling port with a diameter of 140mm, which is connected to the filling port cover with a diameter of 160mm thread and sealed with EPDM or FPM sealing rings. The filling cover is equipped with a sampling cover and anti-theft cover to facilitate sampling. The filling cover and sampling cover are sealed with EPDM or FPM sealing rings. The anti-theft cover uses a disposable buckle and tear type anti-theft cover. An efficient pressure reducing valve is installed in the middle cover of the cover to release the gas volatilized by the liquid product or the pressure change caused by the volume change of the air in the upper part of the container during thermal expansion and contraction. The pressure reducing valve uses a breathable film to block the liquid through the air, and the pressure reducing valve and the sampling cover are sealed tightly with a taper. The container cannot withstand internal pressure. The selection of materials for various parts takes into account hygiene and corrosion resistance to liquids such as acid, alkali, and oil.
Advantages of 1000-liter IBC tank compared to 200-liter double ring drums
IBC TANK and 200-liter double ring plastic drums are two types of packaging containers commonly used in industries such as chemical, food, and daily chemical. Generally speaking, IBC tank have the best cost control compared to plastic and iron barrels, with one ton barrel filling capacity equal to five 200-liter plastic drums filling capacity. And four 200 liter plastic drums occupy the same volume, but can only hold 800 liters of material. A IBC TANK needs to be filled once, sealed once, and labeled once, while a IBC TANK (5 200 liters) needs to be filled 5 times, sealed 5 times, and labeled 5 times. So, IBC packaging not only saves costs but also improves customer work efficiency.
Advantages of IBC TANK : IBC TANK are composed of an inner container and a metal frame, and the inner container is made of high-density polyethylene blown molding, which has high strength and corrosion resistance. The outer metal frame is relatively reliable, and using IBC TANK can significantly reduce production, storage, transportation, and operating costs. Save manpower and material resources. Compared to traditional packaging, storage can save more than 30% of space, and forklift loading and unloading can reduce manual handling. Filling: 1 IBC TANK =5 200L drums, reducing repetitive operations during the filling process while avoiding waste and pollution caused by leaks and spills during the filling process.
In short, IBC tank are more convenient to use, economical and durable, and container barrels can become the mainstream product for liquid packaging. It can hold Class II and Class III dangerous goods, with a maximum liquid density of 1.5g/cm3 for Class II dangerous goods and 1.8g/cm3 for Class III dangerous goods. It can be directly loaded and unloaded with a forklift, and can be stacked for storage. The bottom is equipped with a drain valve, which facilitates, quickly, thoroughly, and safely discharging liquids. It is easy to clean and can be reused multiple times, which is beneficial for environmental protection.
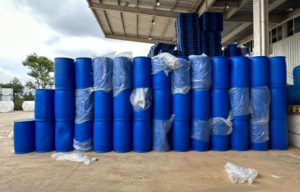

Introduction to the production line of IBC ton barrel blow molding equipment:
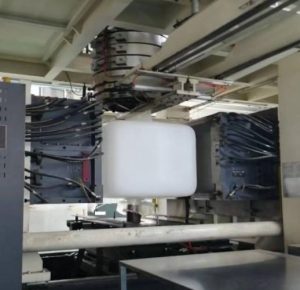
Basic specification:
1、Product specification: 1-3 layers IBC machine. Make sure even wall thickness.
2、HDPE Material: HMWHDPE, HDPE, ABS, PP, PVC, and so on.
Meanwhile we can offer some ripe formula of material to reduce cost but ensure quality
3、Power consumption
Total power | 500kw |
Consumption | 250-280kw |
4 、Machine weight and dimension
Weight | 60 T |
Dimension(L × W × H) | 10× 5 ×7 meter |
5 、Output: 20-24 pcs per hour
1. Extrusion System
1.1Screw:
Top brand in China. [MadeinNANJING]
According to the processing performance of the raw material
Diameter | 110mm 120mm 110mm |
Material | 38CrMoAlA alloyed |
L/D | 30/1 |
Hardness | ≥ 800 |
Brittleness | ≤ grade 2 |
1.2 Screw barrel
1) Made by ourselves.
2) Material: High quality nitriding structural 38CrMoAlA,nitriding
3) Treatment
4) Hardness HV ≥ 900
5) Brittleness ≤ grade 2
1.3 Driving mode:
Siemens AC motor (Not Beide)
There are two types of Siemens in China.One is low standard named BEIDE,another one is imported standard real SIEMENS.
Hard gear reducer controlled by Siemens converters running speed can adjusted through HMI.
Driving power(AC) | 90kw 110kw 90kw |
Plasticizing capacity | 600kg/h |
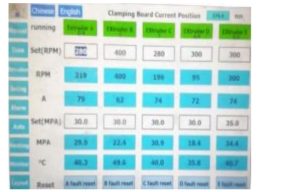
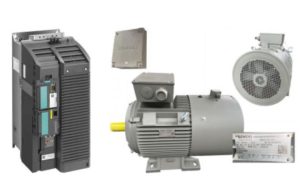
1.4 Reducer
Hard tooth surface ·GUOMAO reducer with high torque from China.
1.5 Heating mode
Cast Aluminum heater with jackets, sections temperature control of each extruder.
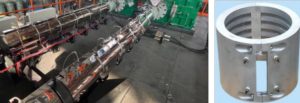
Sections | 18 |
Heating power | 100kw |
Heaters consumption | 30kw |
Cooling way | Automatic independent air cooling |
Material feeding section | Water cooling |
2. Material loader
Vacuum loaders with 3 pcs of 75kg stainless steel material hoppers.
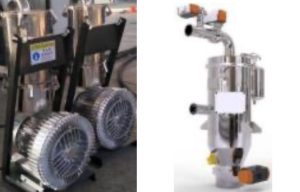
3. Die head system
1) Patented technology die head which produced in our own factory.
Accumulator capacity | 45kg |
Material | 38CrMoAl |
2) The patented transverse wall thickness control system, a manual PWDS system, easy to operate, one single person can operate.
3) Special set of Die-Core pin for IBC.
4) Heating mode: Mica heaters.
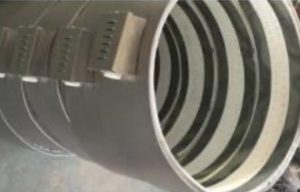
Heating power | 80kw |
Heaters consumption | 24kw |
Manual PWDS made by ourselves Advantage:
1.It can adjust transverse wall thickness by operating bolts on die core pin.
2.ComparedwiththePWDS systemproducedin Germany, the accuracy of adjusting the thickness through bolts is higher. In other words, the control area of each bolt of our manual PWDS system is
smaller than that of the German electric PWDS, and we are equipped with a lot of bolts.
Other supplier ever tried to copy this technology but failed.
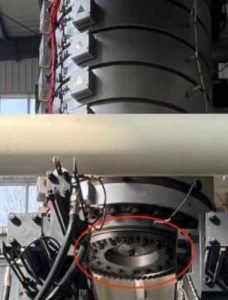
4. Clamping system
4.1 Adopts double linear guide rail moving die system, total 3 cylinders. Single oil cylinder quick mold closing, reverse double oil cylinder powerful mold locking structure,balanced force, small deformation, fast and stable mold moving;
4.2 Clamping structure:two pull rods, center directly pushing,equipped with auto lubrication system which can lubricate blocks and guide rails regularly.
4.3 One whole thick steel plate for pressure holding on back side of diagonal pull rod, ensure clamping unit can hold the maximum clamping force .
1) Jeffran liner scale for platen location limited. Adjust mold location on PLC
.
2) HIWIN linear guide rail
3) HIWIN slider block HG65
Platen size(W*H) | 1600× 1800×90mm |
Max. mould size(W*H) | 1400× 1500mm |
Clamping force | 1700KN |
Clamping cylinder stroke | 2000mm |
Distance between platen | 1000-2650mm |
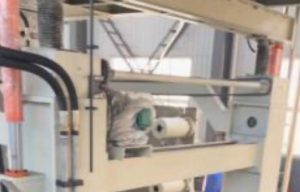
Machine Frame
1) With lifting function, driven by hydraulic with
GUOMAO reducer.
2) Multi-link premium system with auto stop sensor to make height of extrusion system
adjustment more effective.
3) Large lifting stroke, adapt to mold change, maintenance or repairing.
5、Hydraulic system
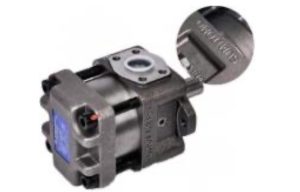
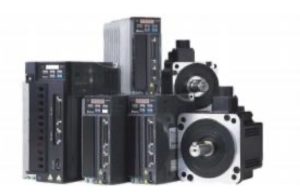
1) The hydraulic system adopts Delta servo flow pressure control, Sumitomo gear pump
2) Each oil pipe will have independent friction protection to ensure a longer service life
Oil tank capacity | 1000L |
Pump | 163CC |
Servo motor | 48kw |
3) Equipped with Yuken hydraulic valve, which has the characteristics of fast and stable action, accurate repeat positioning, long service life and good response.
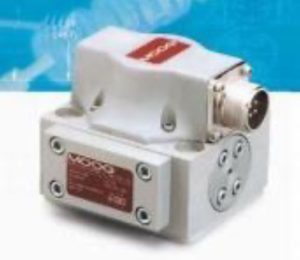
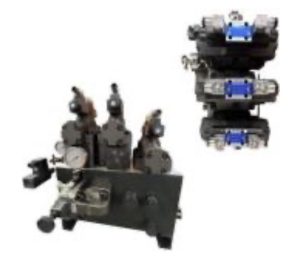
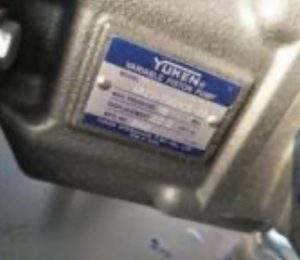
4) Wall thickness control system adopts position and speed double closed-loop design, equipped with 100/200 points optional MOOG thickness controller and MOOG valve.
5) Wall thickness hydraulic system adopts Delta/Inovance servo flow pressure control,Yuken oil pump, filtration precision 3um.
Parison control motor | 7.5kw |
Pump | AR22 |
6、Electric system
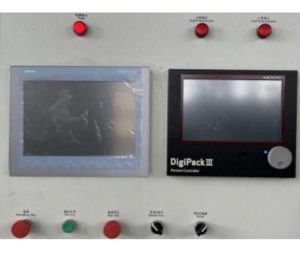
1) The electrical control system adopts Siemens PLC to control the motions program of the whole machine. 2) 12’ Siemens LCD and touch screen are used for communication, parameter setting, modification.
3) Process and parameters can be set and modified directly.
4) The movable form of the swing arm mode can be designed freely.
5) Intermediate relay: Schneider
6) Breaker: Schneider
7) Magnetic exchange valve: YUKEN
Temperature Control
Temperature control components: Siemens
automatic temperature control module equipped with Omron manual temperature control meter for each heater.
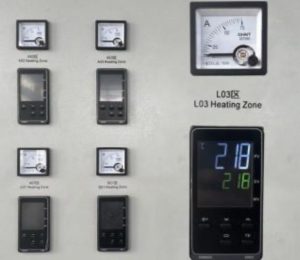
Thermo-relay using Brand Schneider.SSR type.
Advantages of solid-state relay
(1) High life and high reliability.
(2) High sensitivity, low control power and good electromagnetic compatibility.
(3) Fast conversion
(4) Small electromagnetic interference
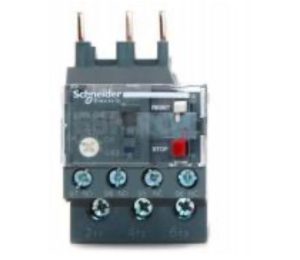
7. HMIPAGE
1) Real time control of machine action.
2) Smooth and stable speed regulation of extrusion motor.
3) Equipped with faults diagnosis display and alarm function.
4) Various functions can be selected to meet the requirements of producing products with different structures.
5) Real-time production time duration timing system.
6) Remote parameter correction system
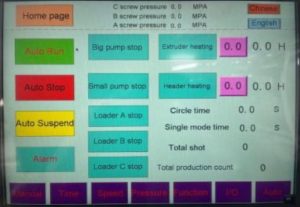
8. Pneumatic
1) Pre blowing, inflation pressure is adjustable.
2) Blow pin: Depend on products.
3) Expand stroke: Accordingly.
4) Maximum air pressure 0.8Mpa
5) Air consumption 1.5 m3/min
6) Explanation: With pre-blowing function, air blowing pin independent design which realize convenient replacement and multiply usage.
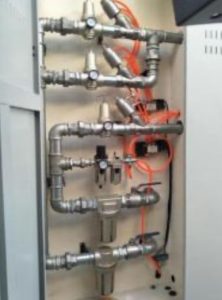